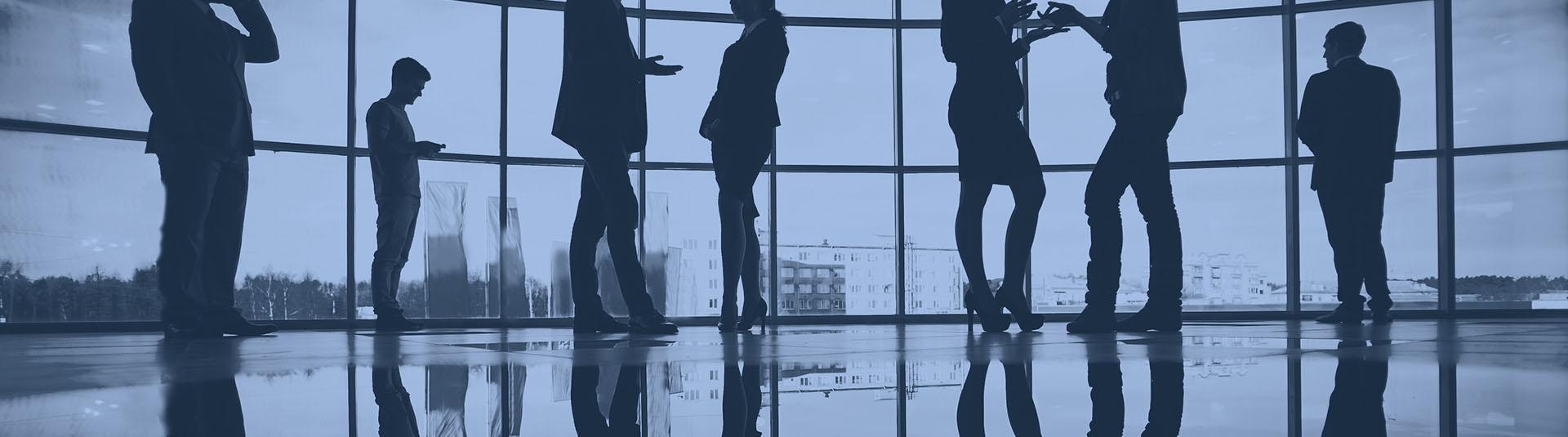
Delivering scope on time
PROJECT MANAGEMENT
guaranteed Results
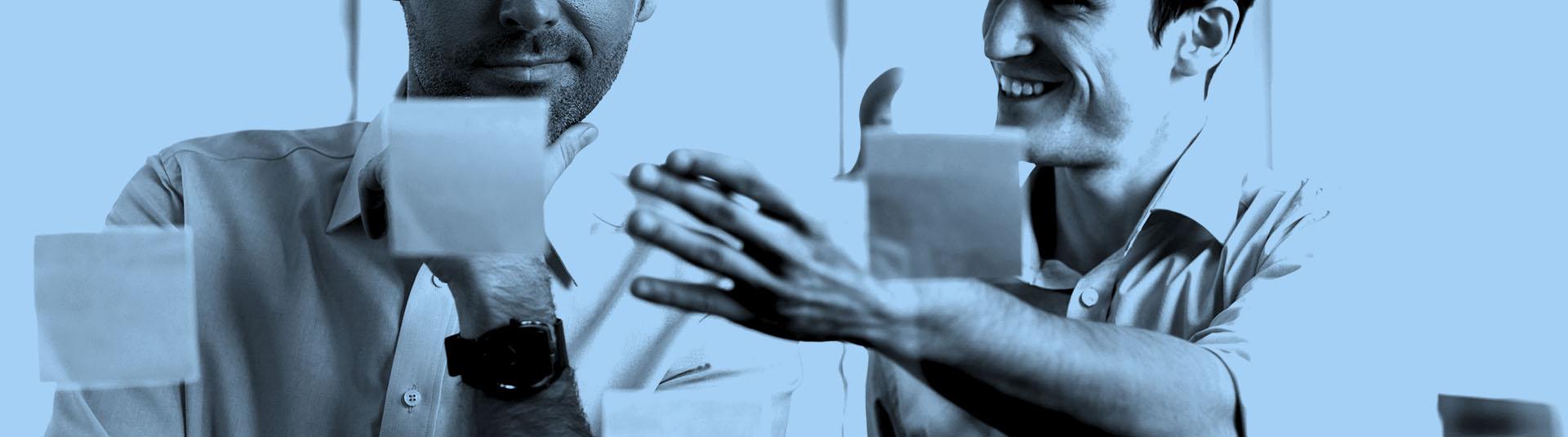
Managing actions and expectations
CHANGE CONTROL
Outcomes achieved
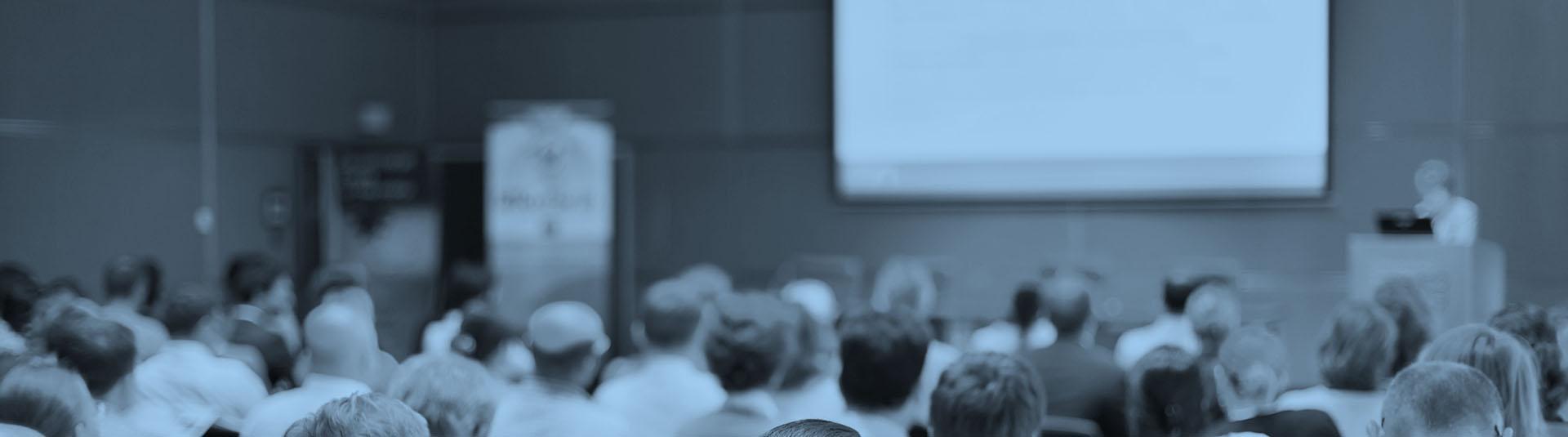
Project Control, Communication skills
TRAINING COURSES
Improved skill base
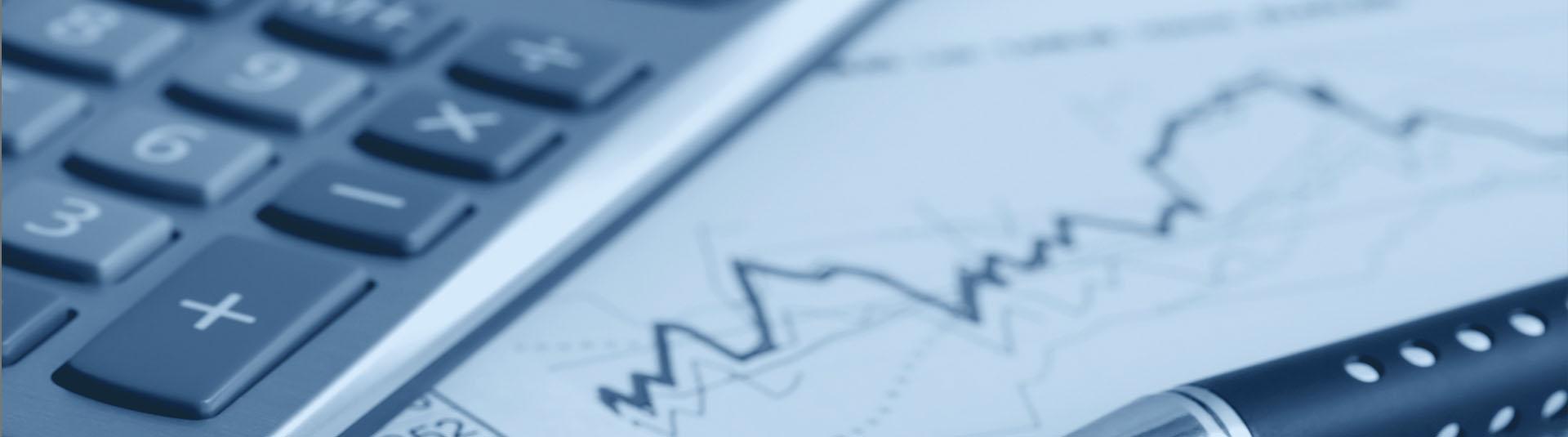
Effective Project Control Services
Dailey Consultancy Ltd